CORPEX® Core Plate Heat Exchangers
Our proprietary plate-type heat exchangers – developed, fabricated and supplied by APEX Group – are heavy-duty exchangers made to handle large volumes of gases for heat recovery and gas treatment applications.
Customized Heavy-Duty Heat Exchangers
The heat transfer core of the CORPEX® heat exchanger consists of smooth flat plates, which create alternating passages for two fluids to travel through. To prevent leakage of the higher-pressure fluids into the lower-pressure fluids, welding is used to seal the plates along the edges.
The CORPEX® heat exchanger uniformly distributes the fluids between the plates, and across the entire width of the plates. This ensures that the flow separation is kept to a minimum and that the velocity profile is well defined; there is a thin laminar sub-layer adjacent to the wall and a turbulent flow core. However, if it is beneficial for the customer’s use-purpose, the thin laminar sub-layer can be agitated by adding VORTI-FLEX® Technology.
APEX Group offers flexibility for CORPEX® plate-type heat exchanger designs; the heat transfer core can be arranged in a cross, co-current or countercurrent flow. Furthermore, we ensure that the design and manufacturing is in accordance with our proprietary techniques.
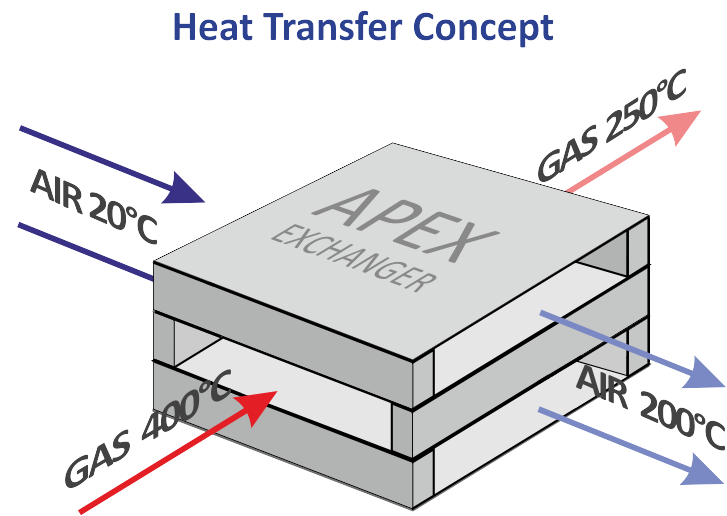
Key Features
Characteristics:
- Constructed from flat plates
- High thermal effectiveness
- Flexible and compact design
- Virtually zero leakage between sides (fluid to fluid) when fully welded, up to 0.5% leakage between sides when clamped
- Low pressure drop
- Minimized fouling tendency
- Easy to clean
- Minimized heat transfer plate erosion
- Virtually unlimited metallurgy choices
- Good response to thermal shocks and heat cycles
- Suitable for working with corrosive (condensing) fluids (with A-CORREX® Technology)
Fluids Handled:
- Combustion Air
- Flue gas from combustion of: gaseous fuels, liquid fuels, solid fuels, waste, biomass
- Vapor (condensing or non-condensing)
- Industrial exhaust streams
- Combustion Air Preheater
- Gas-Gas Heater
- Flue Gas Cooler/ Condenser
Typical Technical Specifications:
- Heat Transfer Plate Thickness: 0.8 to 6 mm
- Design Temperature: Up to 900 °C
- Design Differential Pressure: Up to 0.5 barg
- Duty Range: Unlimited
- Thermal Effectiveness: ~97%
- Pressure Drop Rates: 0 to 0.1 barg (max. 0.5 barg)
- Leakage Rates: Virtually 0%
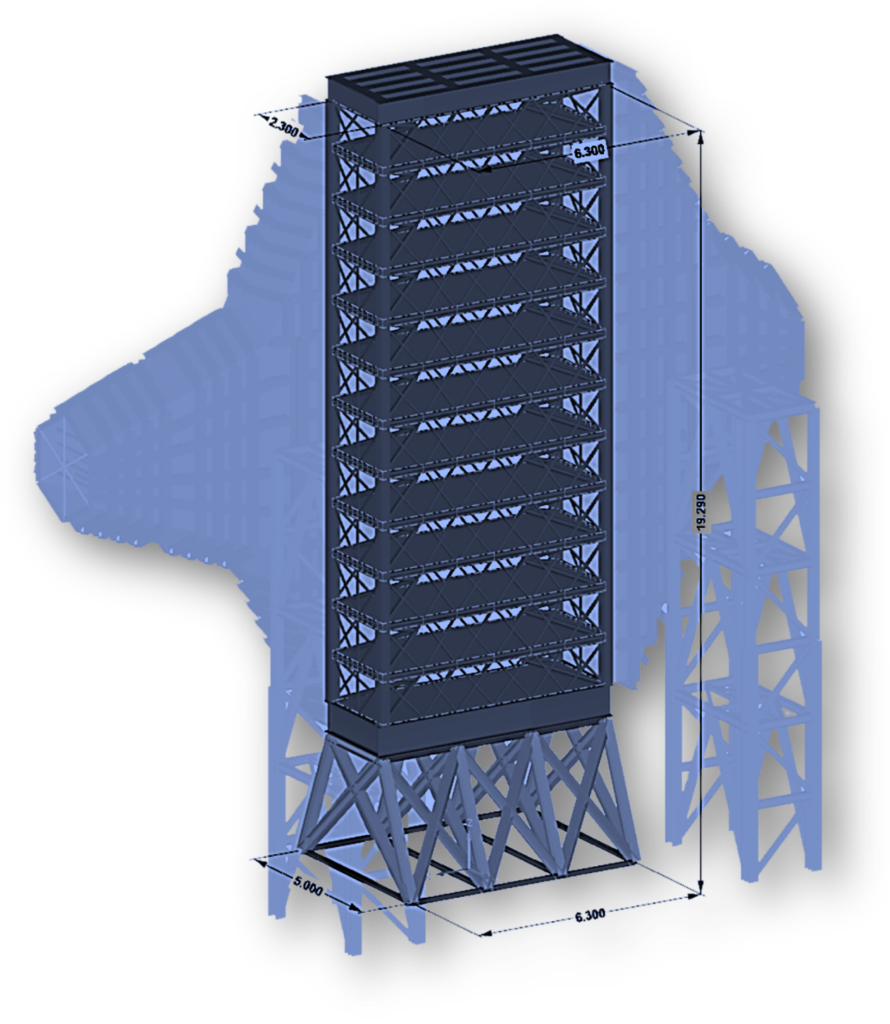
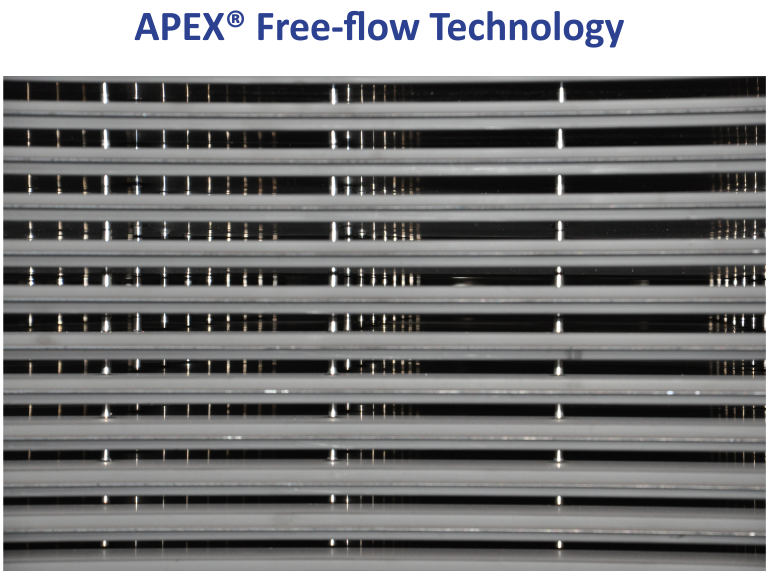
Applicable Technologies:
- APEX® Free-flow Technology – minimizes the flow separation & fouling tendency; this makes the product easier to clean.
- AIR CURTAIN® Technology – controls the heat transfer surface temperature to avoid “cold corner” corrosion.
- APEX® VariaFlow – ensures a uniform flow-field temperature profile at the fluid outlet.
- APEX® Erosion Technology – improves the heat transfer elements’ ability to withstand erosion.
- A-CORREX® Technology – prevents acid dew point and water dew point corrosion.
- APEX-delfino® Technology – optimizes the fluid flow distribution and temperature profile.
- VORTI-FLEX® Technology – enhances the heat transfer coefficient between two fluids in laminar or transient flow.

User Friendly Units
- Easy maintenance
When operating under normal conditions, the heat exchanger does not require any additional inspection or operator attention. However, it is recommended that periodic observation is conducted at the regular plant shut-down intervals. This will help to detect and correct any unusual behavior. - Easy cleaning
APEX® Free-Flow Technology reduces the risk of fouling and improves accessibility to the process channels, making the product easy to clean. It is recommended to clean the unit at regular shut-down intervals. APEX Group can supply permanent acoustic or water cleaning devices for applications with a high fouling potential. Flexibility in flow arrangement due to modular design
Our large heat exchanger units are modular designs constructed from multiple elementary blocks. This modularity allows the heat exchanger to be designed with flexibility, enabling the fluids’ flow direction to be arranged in accordance with the specific installation’s requirements. The elementary blocks are optimized in size for cost-effective transportation and to minimize the complexity of erection in the field.