A-CORREX® Technology
The green transition provides the impulse to decrease the exhaust flue gas temperature below the acid dew point (ADP) because of its positive environmental impacts. This guides APEX Group’s innovation: we seek to develop innovative technologies which enable energy-intensive industries to shift their operations towards reliable and cost-effective functioning under corrosive conditions.
The Formation of Corrosive Acid
Lowering the temperature of flue gas exiting the stack and recycling the heat has positive effects. On the one hand, it reduces operational costs. On the other hand, it improves resource-efficiency (important for meeting increasingly stringent emission-reduction targets: lower fuel consumption decreases total emissions).
However, there is one key limitation to lowering the exiting flue gas temperature: at temperatures below 150°C the sulphuric acid in flue gas condenses. This acidic condensate is corrosive; it damages heat transfer surfaces leading eventually to mechanical failure.
Thus, current air preheating systems are typically designed to have a minimum metal temperature close to, but slightly above, the acid dew point of the flue gas.
A-CORREX® Technology: A Solution for Operation under Corrosive Conditions
The standard metallic materials often used in heat exchange processes are not resistant against acidic corrosion.
APEX Group, however, offers a solution to the limitations presented by the ADP through its development of A-CORREX® technology: we offer a range of heat exchangers which can function in the highly corrosive environments as depicted in region A and B of figure 1.
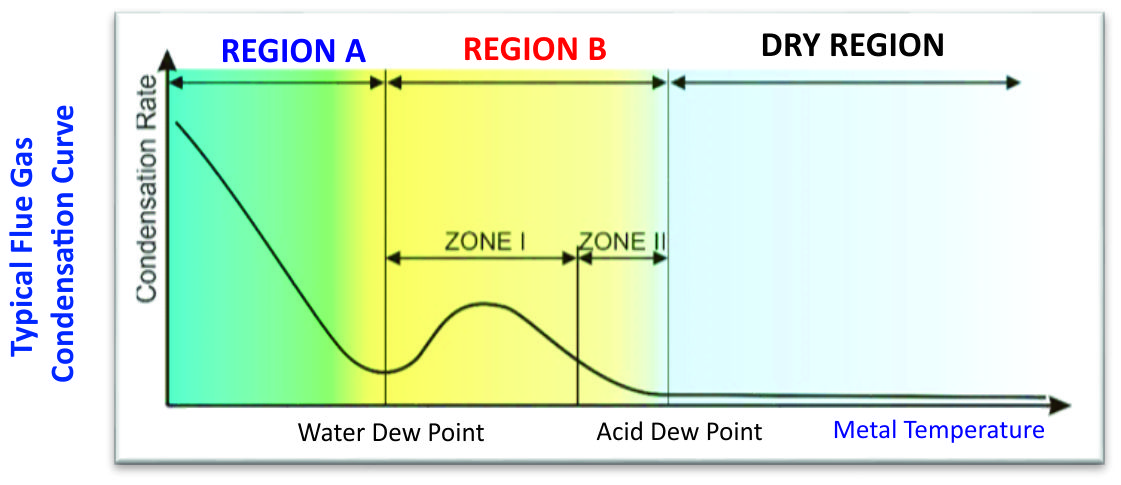
Figure 1. Dew Point Condensation regions for a typical flue gas.
Construction Materials
To manufacture heat exchangers capable of resisting corrosive environments, APEX Group uses the following construction materials for the heat transfer elements:
- PPS-GR composite
- Metallic substrates enameled with borosilicate glass
- Metallic substrates with polymer lining
- Steel alloys
Key Benefits of Each Material
Polymer composite: PPS-GR
- Resistant to virtually any chemical attack below the acid and water dew points;
- Lightweight;
- Operating temperature up to 200 °C (short-term peaks: 220 °C);
- Very resistant to heat cycles; and
- High thermal conductivity > 3 W / m-1 K-1.
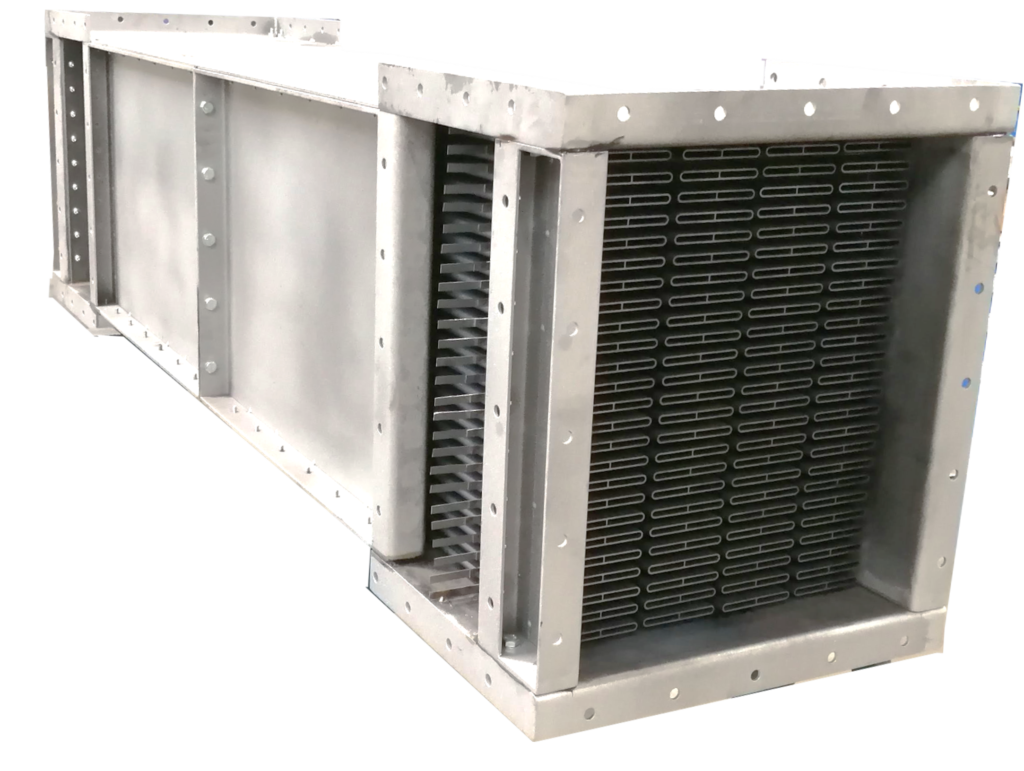
Metallic substrate enamelled with borosilicate glass
- Borosilicate glass enamel ensures protection of metallic substrates against attack of sulfuric acid condensate;
- Operating temperature up to 400 °C;
- Operating pressure up to 0.5 barg for non-pressure vessel, virtually no limit for pressure vessel;
- High thermal conductivity of metallic substrate;
- Resistant to thermal shocks and heat cycles (they can resist temperature variations up to 400 °C);
- Remarkable resistance against high differential pressure during operation; and
- Excellent mechanical strength.
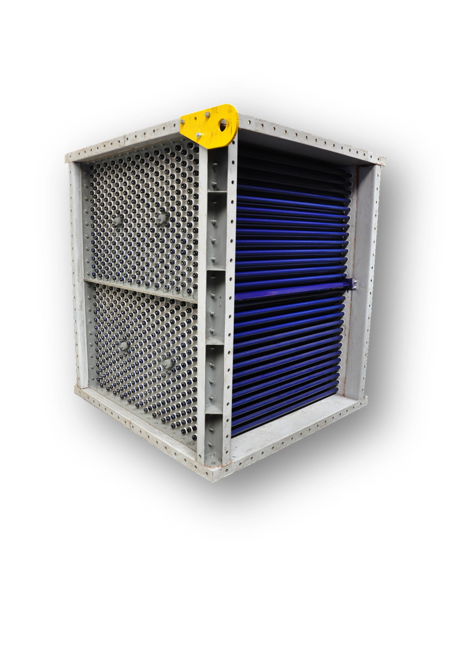
Metallic substrates with polymer lining
- Ensures excellent protection of the metallic substrate against virtually any chemical attack below the acid dew point (but above water dew point) due to the polymer lining (typically PFA);
- Preserves the mechanical strength of the metallic substrate;
- Operating temperature up to 260 °C constant, 350 °C intermittent;
- Operating pressure up to 0.5 barg for non-pressure vessel, virtually no limit for pressure vessel; and
- Resistant to thermal shocks and heat cycles.
Steel alloys
- Satisfactory-to-excellent corrosion resistance for selected acids or alkalis at limited range of concentrations and temperatures;
- Excellent mechanical strength and integrity;
- Operating temperature up to 600 °C;
- Operating pressure up to 0.5 barg for non-pressure vessel, virtually no limit for pressure vessel; and
- Resistant to thermal shocks and heat cycles.